Moulage par injection de pièces en plastique, conseils pour optimiser le processus de moulage par injection de plastique par la conception.
LOCALISATION DES EXTRACTEURS ET DES POINTS D’INJECTION.
Si possible, les extracteurs et les points d’injection doivent être situés dans des zones non visibles de la pièce, car ils influencent l’esthétique finale du produit.
CONTRACTIONS.
Il est important de tenir compte du retrait et de la rétraction du matériau dans la conception des pièces, étant donné le processus de solidification que subit le matériau. Le rétrécissement affecte la précision dimensionnelle de la pièce, mais pas seulement, il introduit également des contraintes internes qui peuvent rendre la pièce invalide. Le taux de rétraction de la pièce est donné par le fabricant du matériau et doit être utilisé dans la conception de la pièce. Le tableau suivant présente quelques valeurs indicatives des pourcentages de rétrécissement subis par différents plastiques thermoplastiques.
THERMOPLASTIQUES | |
Matériau | % de rétraction pendant la solidification |
Acetal POM | 2,0 – 2,5 |
PMMA Acrylique | 0,3 – 0,8 |
ABS | 0,3 – 0,8 |
Polyamide PA | 0,3 – 1,5 |
Polycarbonate PC | 0,5 – 0,7 |
Polyéthylène PE | 1,5 – 5,0 |
Polypropylène PP | 1,0 – 2,5 |
Polystyrène PS | 0,2 – 0,6 |
PVC rigide | 0,1 – 0,5 |
PVC flexible | 1,0 – 5,0 |
ÉPAISSEUR DE LA PAROI
L’épaisseur de la paroi dépend du matériau à injecter. L’épaisseur minimale est limitée par le fait que, dans les parois minces, le matériau a des problèmes d’écoulement, se solidifie (ou durcit) avant de remplir complètement le moule, ce qui augmente la probabilité d’emprisonnement de l’air. Dans les pièces plus petites, l’épaisseur peut être plus faible car le chemin d’écoulement est également plus petit. D’autre part, des épaisseurs plus importantes entraînent des temps de solidification plus longs, un retrait accru et donc des contraintes internes plus importantes. Le tableau suivant indique les épaisseurs maximales et minimales recommandées pour différents plastiques et en fonction de la taille de la pièce.
Petites pièces | Petites pièces | Grandes pièces | Grandes pièces | |
MATÉRIAUX | Épaisseur moyenne | Épaisseur minimale | Gamme d’épaisseurs | Épaisseur moyenne |
Thermoplastiques | moldblade | |||
Acryliques (PMMA, PAN, ABS, SAN) | 0,99 | 0,65 | 3,25 – 6,50 | 2,5 |
Acétates de cellulose | 1,25 | 0,65 | 3,25 – 4,75 | 1,9 |
Acétate de cellulose Butyrate | 1,25 | 0,65 | 3,25 – 4,75 | 1,9 |
Ethylcellulose | 1,25 | 0,9 | 2,50 – 3,25 | 1,6 |
Polyamide PA | 0,65 | 0,35 | 2,50 – 3,25 | 1,6 |
Polyéthylène PE | 1,25 | 0,9 | 2,50 – 3,25 | 1,6 |
Polystyrène PS | 1,25 | 0,75 | 3,25 – 6,50 | 1,6 |
Chlorure de polyvinyle PVC | 2,5 | 1,6 | 3,25 – 6,50 | 2,5 |
Il est toujours recommandé que les épaisseurs soient uniformes, et dans le cas où un changement d’épaisseur est inévitable, la transition doit être douce et non abrupte.


Les fils
Les fils moulés doivent être de la pâte. Pour une bonne conception du moule à injection, il est nécessaire d’arrondir à la fois les crêtes et les vallées pour éviter les arêtes vives et l’inexistence de rayons d’accord.

Les dimensions minimales doivent être de 32 filets par pouce (pas de filetage supérieur à 0,75 mm).
Les douilles filetées sont préférables lorsque le pas est fin, le diamètre petit et lorsque des tolérances étroites sont requises, ainsi que lorsqu’un vissage-dévissage fréquent est nécessaire.
Les sorties de filets doivent être laissées, et pour réaliser de petits filets femelles, il est préférable de laisser un trou et de tarauder ensuite.
HOL HOLES
Ils peuvent compliquer (et donc rendre plus cher) le moule, et ont tendance à former des bavures et des lignes de soudure. L’espacement minimal entre les trous, et la paroi est de 1 diamètre, et commodément à une distance de 3 diamètres de l’extrémité de la pièce pour éviter les tensions, bien que dans le cas des thermodurcissables l’augmentation du diamètre permette de réduire les distances minimales.
Les trous traversants sont préférables aux trous borgnes, car la fixation du robinet en deux points améliore le positionnement et la résistance à la rupture de celui-ci. De plus, il est pratique de donner un petit cône à la base du taraud pour lui donner une plus grande résistance, tout en formant un petit accord à l’entrée du trou.
Il est recommandé que les trous soient perpendiculaires au plan de joint, car les parallèles les obligent à être des noyaux rétractables.
Dans les trous aveugles, il est recommandé, lorsqu’il s’agit de thermoplastiques, de L≤2D ou L=D mm si D≤1,5 mm, et de L≤2,5D ou L≤1D si D≤1,5 de le mettre dans un tableau ou d’une autre manière plus graphique lorsqu’il s’agit d’un thermodurcissable. Pour augmenter la profondeur, utilisez des trous étagés.


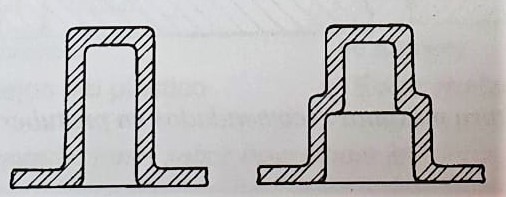
NERVEAUX
Ils doivent être utilisés pour réduire l’épaisseur du mur qu’ils renforcent, mais il faut tenir compte d’une série d’aspects. Ils doivent être plus fins que le mur qu’ils renforcent pour éviter les marques. Il est recommandé que tnerves ≤ 0,5-tmur. Les nerfs doivent avoir une hauteur inférieure à 1,5-tmur pour éviter les marques. Pour obtenir l’effet de renforcement nécessaire avec cette hauteur, la nervure peut être divisée en deux plus petites séparées par une distance égale à deux fois l’épaisseur de la paroi. La séparation entre les nervures et le mur doit être supérieure à 2-tmur. Les sorties des côtes doivent être généreuses (5°).
Les côtes doivent être perpendiculaires au plan de joint. Vous pouvez masquer les marques de côtes en utilisant des textures.

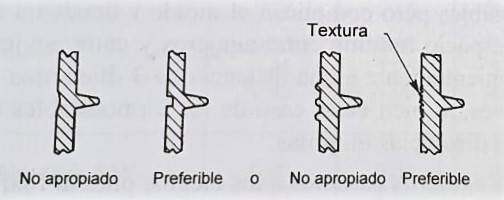
BUMPS
Pour les protubérances, les mêmes règles que pour les nervures s’appliquent, mais dans ce cas la hauteur maximale recommandée est de 1,5-tmur et la largeur doit être inférieure à 0,5-tmur.
Si possible, les protrusions doivent être placées dans les coins pour faciliter le remplissage. Si elle est isolée, une nervure est placée pour faciliter le remplissage.
Essayez d’éviter de placer des protubérances au sommet du moule pour éviter de piéger l’air. Si les saillies sont importantes, elles doivent être creusées pour maintenir l’uniformité des murs.
Un angle de 5° doit être utilisé, comme dans les nerfs.

porte-à-faux
Les porte-à-faux qui ne sont pas perpendiculaires au plan de joint nécessitent l’utilisation de moules d’injection à parties centrales coulissantes, avec une augmentation conséquente des coûts. Les bosses externes peuvent être placées sur le plan de joint pour simplifier le moule.
INSERTS
Les inserts sont utiles pour fournir un renforcement localisé. Ils sont généralement peu coûteux, mais ils rendent le processus plus onéreux et doivent être évités.
Évitez d’avoir des bords tranchants de l’insert dans la partie encastrée dans le plastique. Les fentes de l’insert doivent être suffisamment larges pour permettre au plastique d’atteindre toutes les parties.
Les inserts filetés doivent être positionnés perpendiculairement au plan de joint pour simplifier le moule. Les inserts irréguliers doivent être positionnés avec leur axe dans le plan de joint du moule d’injection plastique.
La longueur d’encastrement de l’insert doit être égale ou supérieure à 2-D.
Les inserts sont souvent placés encastrés dans une protubérance. Si le diamètre extérieur de l’insert est inférieur à 6mm, alors Dprotub. ≥2-D ; si le diamètre extérieur de la protubérance est supérieur à 6mm, alors l’épaisseur de la paroi de la protubérance doit être comprise entre 50 et 100% du diamètre de l’insert.
Il est parfois pratique de faire l’insert après le moulage, ce qui évite les problèmes de contamination de la surface de l’insert en contact avec le plastique pendant le processus de moulage, simplifie le moule et élimine la possibilité qu’il soit endommagé par l’insert. Les inserts peuvent être réalisés alors que le matériau est encore chaud, ou avec des techniques à ultrasons.
Pour les inserts filetés, la partie filetée doit être éloignée de la surface pour éviter que le flux de plastique ne l’atteigne. Les chanfreins dans le matériau plastique autour des inserts doivent également être évités.