Para criar qualquer peça em plástico pelo método de injeção de plástico, é necessário um molde metálico, isso é claro.
As perguntas que devem ser consideradas são:
- Como projetar um molde de injeção?
- O que precisa ser levado em conta ao projetar um molde?
- Como um molde de injeção funciona?
Ao construir um molde de injeção de plástico, escolher o número de cavidades pode gerar mais dúvidas. Se a peça de plástico for muito grande (como cadeiras, cercas urbanas, assentos, etc.), a escolha de 1 cavidade é bastante óbvia devido ao seu tamanho. Outro caso são peças para as quais se deseja uma produção em pequena escala, o que não requer um molde mais caro, sendo assim, é escolhida 1 cavidade.
Para produções grandes ou quando é necessário alto volume de produção em pouco tempo, pode-se optar pela opção de multicavidades, permitindo fabricar várias peças na mesma injeção, de acordo com o número de cavidades do molde.
Outro caso claro de uso de múltiplas cavidades é quando é necessário fabricar várias peças pequenas diferentes, em que criar um molde para cada peça seria muito caro. Nesse caso, a multicavidade é a opção mais lógica e econômica.




No caso de ser necessário um molde de injeção com apenas uma cavidade, a distribuição e o design são simples. Mas e quando é necessário um molde com várias cavidades? Como elas são distribuídas? É feito de forma aleatória? Existem maneiras melhores e piores de posicionar as cavidades? O que precisa ser considerado ao projetar um molde?
A resposta é que há toda uma ciência por trás disso e, como em todo o mundo da injeção de plástico, nada é deixado ao acaso.
O primeiro passo é calcular quantas cavidades são necessárias, pois isso definirá a distribuição delas. A regra de ouro para os moldes de injeção com várias cavidades é que sejam o mais simétricos possível, para que o plástico alcance todas as peças e as preencha ao mesmo tempo e de maneira uniforme. Se as cavidades forem distribuídas de forma inadequada, algumas peças serão preenchidas antes das outras, o que pode prolongar o tempo do ciclo ou resultar em peças com resfriamento insuficiente e defeitos. Esse processo de injeção de plástico não é simples, pois quanto mais cavidades forem necessárias, mais complicada será sua distribuição. Além disso, à medida que os canais se tornam maiores, o plástico perde pressão e temperatura à medida que se afasta do ponto de alimentação principal. Nas imagens a seguir, é possível visualizar de forma qualitativa esse fenômeno.
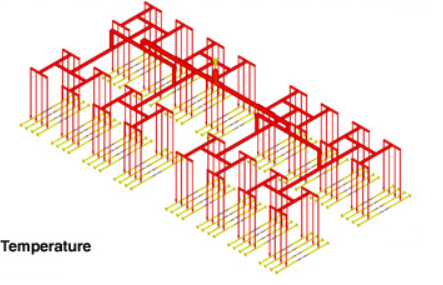

Para projetar o molde de injeção de plástico, é necessário conhecer e responder a estas perguntas:
- Como se mede um molde de injeção?
- Como calcular a área de um molde?
- Como calcular a velocidade de injeção?
- Como calcular a força de fechamento em um molde?
- Como calcular o volume de injeção?
- O que é a cavidade de um molde?
Existem várias maneiras de distribuir as cavidades de acordo com as necessidades do molde de injeção, sempre buscando um fluxo equilibrado e reduzir o consumo de material. Muitos sistemas de alimentação usam uma mistura de designs radiais e ramificados. O design radial tem um volume de sistema de alimentação mais baixo e proporciona um fluxo mais equilibrado. No entanto, são necessários canais primários mais longos e mais resíduos à medida que o tamanho das cavidades aumenta.
Na imagem a seguir, podem ser vistas diferentes tipos de distribuição radial. Como pode ser observado, há uma grande quantidade de opções para a disposição das cavidades, e para escolher a ótima, geralmente são testados diferentes tipos de distribuições e são realizadas análises de preenchimento para verificar seu comportamento.

Outra forma igualmente válida é posicionar as cavidades com linhas retas criando ramificações. Deve-se notar que, enquanto para o tipo radial o número de cavidades pode ser par ou ímpar, para o tipo de ramificação o número de cavidades deve ser par, caso contrário, estaria desequilibrado.

Embora existam várias formas de posicionar as cavidades em um molde de injeção de plástico, nem todas são aceitáveis ou podem ser melhoradas, pois as cavidades nos planos do molde de injeção, embora à primeira vista possam parecer simétricas e válidas, ao pensar cuidadosamente, a colocação fará com que as peças não sejam idênticas umas às outras. Nos exemplos a seguir, a disposição à esquerda está incorreta e a da direita é a melhoria.
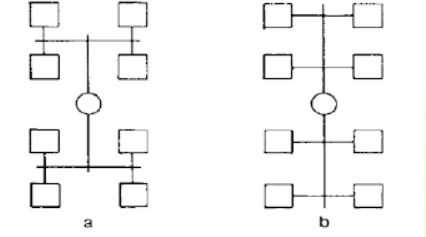
Neste primeiro caso, é bastante evidente que na imagem da esquerda o fluxo não alcançaria simultaneamente todas as cavidades. Primeiro chegaria às 4 cavidades mais próximas ao bico do molde de injeção e, posteriormente, às outras 4 mais distantes, criando peças desiguais. Isso pode ser resolvido alterando a distribuição, como mostrado na imagem da direita. Com essa mudança, todas as cavidades saem idênticas.
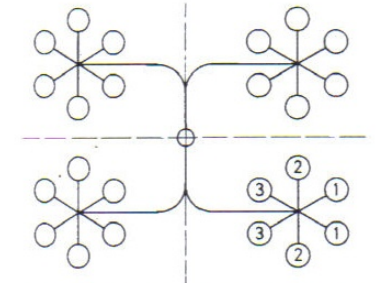

No segundo caso, parece que a distribuição está correta, pois é simétrica e parece que o fluxo chega simultaneamente, mas é preciso considerar não apenas a distância, mas também a direção. É necessário lembrar que é um plástico derretido e tem uma inércia. Portanto, as cavidades com o número 1 serão as primeiras a serem preenchidas, depois as que têm o número 2 e, por último, as que têm o número 3, criando desigualdades. Isso pode ser melhorado alterando a distribuição para a imagem à direita, na qual tanto a distância para cada cavidade quanto a forma de entrada do fluxo são iguais.
Outra maneira menos recomendável de equilibrar o fluxo nas cavidades é aumentando ou diminuindo os canais de alimentação. É uma prática que, embora possa ter sucesso, também pode acarretar problemas. Os sistemas de alimentação naturalmente equilibrados (pela distribuição de cavidades) fornecem maior consistência de cavidade para cavidade em relação ao fluxo de fusão, pressão de fusão e qualidade da peça moldada do que os designs equilibrados artificialmente (modificando o diâmetro dos canais ou entradas).
Esta prática é especialmente utilizada na fabricação de diferentes peças pequenas de plástico em um mesmo molde de injeção de plástico. Com esta prática, é possível produzir muitas peças de um conjunto, com o único custo de fazer um molde em vez de ter que fazer um para cada peça, resultando em uma economia significativa. Logicamente, é necessário fazer cálculos para que todas as cavidades estejam equilibradas, então, em princípio, ter todos os canais e entradas iguais não seria uma colocação ideal.

A diferença entre um molde de injeção de plástico equilibrado e um desequilibrado é bastante notável. Na primeira imagem, observa-se um tempo de preenchimento de 10,24 segundos e um preenchimento irregular, enquanto na segunda imagem, com entradas balanceadas, nota-se um preenchimento uniforme e um tempo de preenchimento significativamente menor, 8,04 segundos. A diferença é de mais de 2 segundos.


Uma vez tomada a decisão sobre como posicionar as cavidades, é necessário considerar o tamanho adequado dos canais que alimentam todas as cavidades. Logicamente, os canais não têm diâmetro constante; no início do sistema, são consideravelmente maiores do que à medida que se ramificam, já que o fluxo de plástico que devem transportar é menor à medida que se afastam do bico de injeção principal. Tê-los todos do mesmo tamanho seria ineficaz, pois requereria mais plástico para cada injeção, e além disso, esse plástico seria desperdiçado. Aumentar o tamanho dos canais faria com que tivessem uma área de contato maior com o metal do molde, fazendo com que o plástico esfriasse rapidamente, podendo obstruí-los.
Se você tiver dúvidas sobre o design das cavidades em um molde de injeção, na Moldblade somos especialistas em Design, Fabricação de Moldes e Fabricação de Peças Plásticas por meio de Injeção de Plástico