Para las empresas especializadas en la inyección de plásticos, comprender y optimizar este ciclo es esencial para mantenerse competitivas en un mercado que constantemente busca mayor rapidez, eficiencia y calidad. El ciclo de inyección es la parte productiva de la inyección de plásticos, donde se convierten las ideas de diseño y la producción de moldes en productos tangibles.

Este ciclo está compuesto de diversas fases en las que se invierte un tiempo, algunas son independientes entre sí mientras que otras se hacen de forma simultánea, la suma de todos esos tiempos resulta en el tiempo de ciclo. El objetivo que se persigue es conseguir un tiempo de ciclo completo lo más bajo posible, ya que de esta manera la cantidad de piezas producidas en una misma cantidad de tiempo será mayor.
A continuación, se explican las fases y los tiempos empleados experimentalmente para un molde de dos cavidades que genera unas probetas de ensayo en polipropileno.
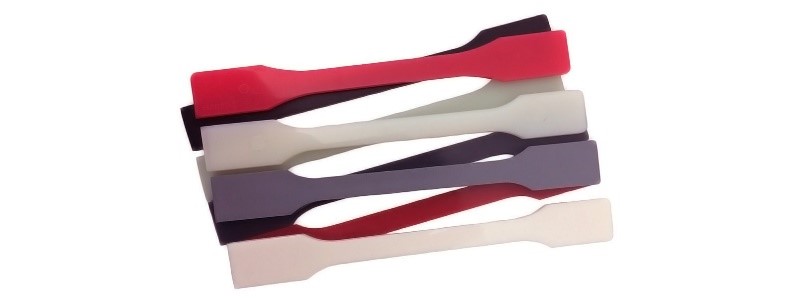
Los números entre corchetes indican el tiempo en segundos empleado en cada fase en el acumulado del total.
[0-1] Cerrado de molde: A partir de este momento, se pone en marcha el cronómetro que contabiliza el tiempo que durará el ciclo. Primero, se da comienzo al ciclo de inyección con el cierre del molde. En esta fase se cierra el molde colocando cada pieza metálica en su sitio para que cuando se inyecte el plástico se genere la forma deseada. Esta fase no solo implica el alineamiento físico de las piezas del molde, sino también la preparación térmica, asegurando que el molde esté a la temperatura adecuada para evitar deformaciones en el producto final.
[1-2] Acercamiento de la unidad de inyección: Se acerca la unidad de inyección con el plástico ya en temperatura y a la presión calculada óptima a la boca de entrada del molde, asegurando que el material fluya correctamente hacia las cavidades del molde.
[2-2.7] Llenado: Esta fase parece que simplemente es introducir el plástico deseado en las cavidades del molde, pero va mucho más allá. El llenado lleva un estudio previo para que llegue a todos los lugares de las cavidades y no queden partes por rellenar debido al atrapamiento de aire y al enfriamiento, además de que no se produzcan otros defectos.
Se puede realizar en uno o en varios puntos diferentes para favorecer el llenado de la pieza especialmente en piezas de gran tamaño. En esta fase es crítica la precisión entre la temperatura tanto del plástico como del molde, la velocidad de inyección y la presión de inyección.
[2-30.7] Enfriamiento: Este proceso empieza en el mismo instante que se inyecta el plástico, ya que, desde que sale del husillo se va enfriando cada segundo, especialmente cuando entra en contacto con el molde, que siempre está más frío que el polímero que se inyecta. Además, este proceso es el suele ser el más largo del ciclo, así que es vital reducir este tiempo lo máximo posible. Esto se puede hacer con refrigeración en el molde, esto es, optimizando los circuitos de agua que discurren por el interior del molde para maximizar la transmisión de calor del plástico al metal y de éste al agua que discurre por los circuitos. Estos circuitos deben estar correctamente calculado para que el enfriamiento en la pieza sea lo más uniforme posible y así evitar deformaciones y rechupes por diferente contracción por variaciones de temperatura. El tiempo de enfriamiento depende en gran medida del grosor de la pieza, por lo que debe ser un factor a tener en cuenta en la fase de diseño para no generar ciclos extremadamente largos. Para piezas más complejas o que exigen ciclos más cortos se podrían emplear refrigeraciones con aleación con cobre berilio (CuBe) o similares que al tener mayor conductividad aumentan la transmisión de calor o permiten que el frío llegue a alcanzar zonas donde los circuitos no alcanzan.
[2.7-20.7] Compactación: Este proceso discurre en paralelo con el enfriamiento durante gran parte del ciclo. Una vez el interior del molde ha recibido el material que requiere, el polímero se va enfriando y contrayendo. Por ello, se ha de inyectar una cantidad extra de plástico para poder compensar esa contracción y que no se generen llenados incompletos. Una vez que la presión llega hasta los valores de presión del exterior la fase se acaba, ya que eso significa que el bebedero está solidificado y por ello ya no va a entrar ni salir nada del plástico del molde. Esto es vital para garantizar la integridad y las dimensiones precisas del producto final.
[20.7-21.7] Retirada de la unidad de inyección: Una vez ha finalizado la fase anterior, se procede a la retirada de la unidad de inyección del molde para preparar el siguiente ciclo.
[21.7-22.7] Carga: En esta fase y cuando el husillo ya está separado del molde, se prepara la máquina para la siguiente dosis de inyección del siguiente ciclo. Este paso se da en paralelo al enfriamiento de la pieza. Si la máquina es lenta en carga y la pieza es pesada, el tiempo de carga puede ser lo que marque el momento de poder abrir el molde y no el enfriamiento como habitualmente, por lo que podría dilatar el ciclo.
[30.7-31.7] Apertura de molde: Esta etapa es relativamente sencilla, ya que se abre el molde con la pieza ya solidificada y con la forma final para prepararse para la expulsión. En esta fase, un elemento importante a considerar son las correderas. Las correderas son componentes del molde que se mueven perpendicularmente a la dirección de apertura del molde. Se utilizan para crear características de diseño complejas en la pieza inyectada, como salientes, rebajes o agujeros que serían imposibles de formar con un molde de dos partes estándar.
El movimiento de las correderas debe sincronizarse precisamente con el proceso de apertura del molde. Un mal diseño o una mala sincronización pueden llevar a daños en el molde o en el producto final. Además, las correderas añaden complejidad al diseño del molde y pueden aumentar los tiempos de ciclo, por lo que su uso debe ser cuidadosamente considerado y optimizado.
[31.7-32.7] Expulsión: Esta es la última fase del proceso, como su nombre indica en esta etapa se expulsan las piezas del molde haciendo que caigan para ser recogidas o un robot las extraiga. Hay diferentes formas de hacer que estas piezas se separen del molde. La forma de expulsión puede ser mediante expulsores, mediante placa de expulsión, con aire… Es importante a la hora de diseñar el molde pensar bien la forma de expulsión de la pieza, ya que de lo contrario no se podrá expulsar la pieza del molde o puede salir con marcas y defectos.
En caso de la máquina estar equipada con movimientos paralelos de apertura y expulsión, se puede sincronizar el movimiento de apertura para que conforme vaya abriendo se mueva el cilindro de expulsión de la máquina y permita tirar la pieza mientras la prensa abre. Esto permite arañar unos segundos.
Al poner todos estos tiempos en un diagrama se puede entender más fácilmente. Los números que están en blanco representan el tiempo propio de cada proceso y los que están en negro representan el acumulado.
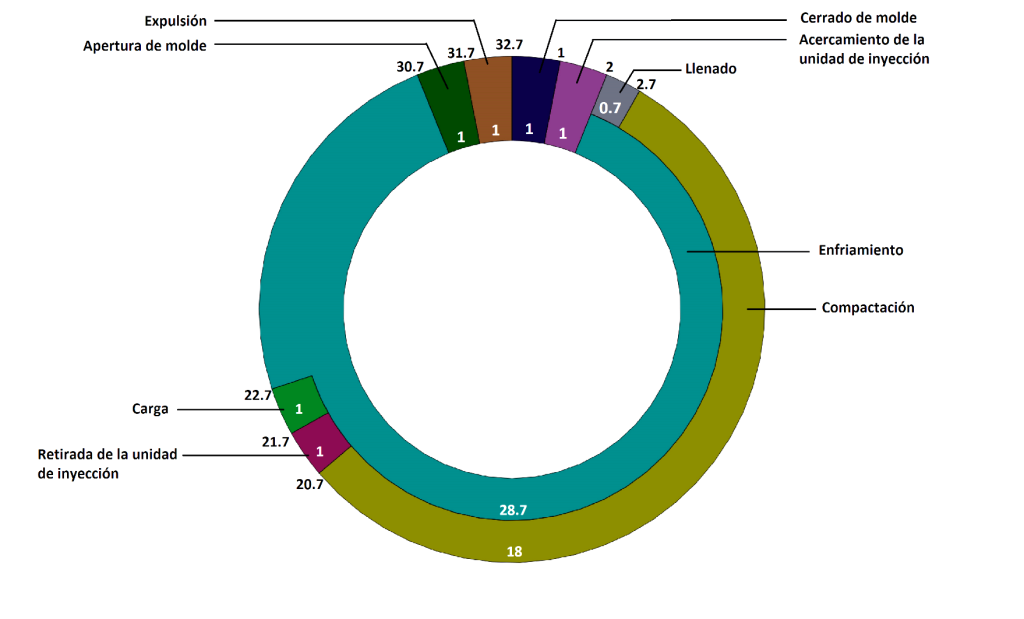
Como se observa en el diagrama el acumulado de tiempos es de 32.7 segundos, esto significa que se necesitan 32.7 segundos para la fabricación de dos piezas completas.
Después de esto, en muchos casos hará falta un postproceso para eliminar rebabas y retirar bebederos que no se contemplan en el ciclo.
Como se ha dicho al comienzo de este artículo, los tiempos de ciclo cambian con cada pieza y, por lo tanto, lo mejor para saber el tiempo de producción para cada pieza concreta es contactar con un profesional. Desde Moldblade podemos realizar los diseños a partir de una idea o una necesidad y encargarnos de todos los cálculos y el proceso productivo completo.