Verzakkingen (Rechupes)
Zinksporen zijn inkepingen in het oppervlak van het spuitgegoten kunststofdeel die ontstaan in de laatste fase of het laatste stadium van het spuitgietproces, tijdens het afkoelingsproces. De dikkere delen van de kunststof koelen langzamer af dan de andere, wat leidt tot een hoger krimppercentage op die plaats. Nadat het materiaal aan de buitenkant is afgekoeld en gestold, begint het materiaal aan de binnenkant af te koelen en het krimpen ervan trekt het oppervlak naar binnen, waardoor een oppervlakteverlaging ontstaat.
Het gebruik van hoge verdichtingsdrukken levert soms aanvaardbare zinksporen op door de volumetrische krimp te verminderen, hoewel deze niet volledig kan worden geëlimineerd. Dit komt doordat de volumeverandering van kunststof van smelt naar vaste stof ongeveer 25% bedraagt en de samendrukbaarheid van kunststof bij de typische spuitgietdruk slechts 15% is, hetgeen betekent dat het onmogelijk is de gesmolten kunststof voldoende te verdichten om de afkoelingskrimp te compenseren.
De volgende ontwerp- en engineeringregels bij het maken van matrijzen en het spuitgieten kunnen dit gebrek tot een minimum beperken:
- El espesor de la pieza de plástico ha de ser uniforme.
- Evitar el uso de puntos de inyección muy pequeños ya que esto evita una correcta compactación del polímero.
- Se han de rellenar las zonas de la pieza más gruesas primero para que éstas sean compactadas antes que las secciones delgadas solidifiquen.
- Incrementar el tiempo de compactación.
- Aumentar la presión de compactación para forzar más material en el molde de Inyección y reducir la contracción.
- Aumentar el tiempo de enfriamiento.
- Modificar la geometría de la pieza para que las depresiones se muestren en áreas en las que tienen un menor impacto en el diseño.
- Reducir la temperatura de inyección del material y el molde. A pesar de que el aumento de la temperatura de inyección de plástico permite una mayor compactación del polímero fundido, las marcas de hundimiento aumentan debido a que aumenta aún más la contracción volumétrica.
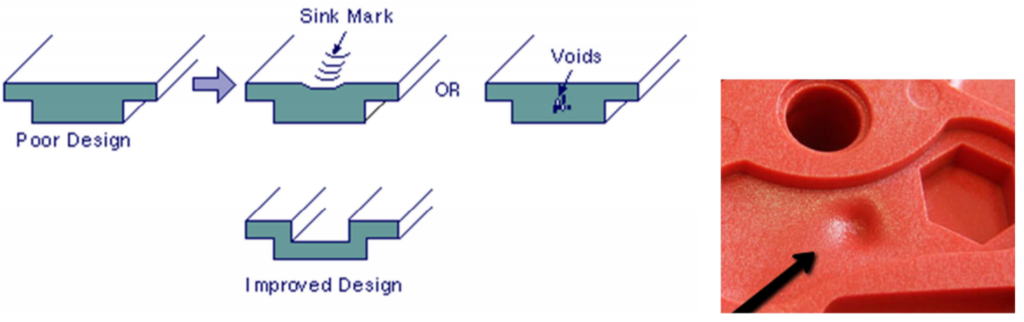
Onvolledige vulling
Onvolledige vulling doet zich voor wanneer een spuitgietproduct te weinig materiaal heeft om de geometrie correct te genereren. Dit gebeurt wanneer de polymeermassa niet de volledige holte (of holtes) van de spuitgietmatrijs kan vullen, meestal de dunnere delen waar de polymeermassa afkoelt voordat zij de matrijs volledig vult. Elke factor die de weerstand aan de voorzijde van de polymeermassa verhoogt, kan leiden tot onvolledig vullen. Enkele van deze factoren zijn:
- Existencia de áreas del molde de Inyección que restringen en exceso el flujo del polímero fundido, como son los canales de alimentación, las puertas de entrada, paredes delgadas, etc.
- Temperaturas de inyección de plástico y de las paredes del molde bajas.
- Existencia de aire atrapado en el interior de la cavidad del molde.
- Presión de inyección del plástico de la máquina insuficiente.
- Solidificación prematura del polímero fundido debido a:
- El fenómeno del “hesitation” o “dubitación”.
- Perfil de inyección incorrecto.
- Tiempo de inyección prolongado.
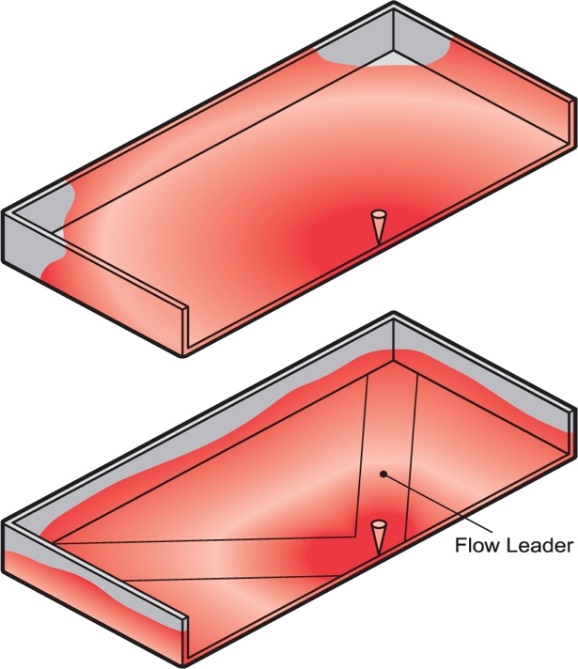
Enkele praktijken die wij in de afdeling Moldblade Engineering hebben ontwikkeld om het probleem van onvolledig vullen te verhelpen zijn:
- Rellenar primero las secciones de la pieza más gruesas antes que las delgadas para evitar el fenómeno del “hesitation” o “dubitación”.
- Las puertas de inyección del plástico se han de situar alejadas de las zonas delgadas de la pieza o zonas con cambios bruscos de espesor.
- Aumentar el número de puertas de entrada para reducir la longitud de flujo.
- Aumentar el tamaño de los canales de alimentación para reducir la resistencia al flujo.
- Colocar zonas de aireación en los lugares adecuados (en las zonas del molde que se llenan al final) para dar salida al airea atrapado.
- Aumentar el tamaño y el número de orificios de ventilación.
- Aumentar la presión de inyección. Para evitar daños al sistema hidráulico de la máquina, se suele limitar la presión de inyección de funcionamiento al 70-85% de la presión de inyección máxima.
- Aumentar la velocidad de inyección. Esto produce un incremento de temperatura y reduce la viscosidad del polímero fundido.
- Aumentar la temperatura de inyección y/o la temperatura de las paredes del molde. Temperaturas más altas reducen la viscosidad del polímero fundido y facilitan el llenado del molde.

Gevangen lucht
Het gebrek aan ingesloten lucht ontstaat wanneer een bepaalde hoeveelheid lucht tijdens het inspuiten niet uit de matrijs kan ontsnappen, waardoor een klein gebied zonder materiaal in het gespoten onderdeel ontstaat. In een correct ontworpen spuitgietmatrijs wordt de lucht bij elke injectie uitgestoten via de matrijsopeningen, matrijsinzetstukken of zelfs uitwerpers, die ook als openingen fungeren.
De locaties van de ontluchtingsgebieden in de matrijzen bevinden zich in de gebieden die aan het einde van de cyclus of injectiefase worden gevuld. Een veelvoorkomende oorzaak van een ingesloten luchtdefect zijn ondermaatse vormopeningen. Een andere veelvoorkomende oorzaak is wanneer het «racetracking»-fenomeen optreedt (de neiging van de polymeersmelt om bij voorkeur in dikkere secties te vloeien, waardoor dunnere gebieden met ingesloten lucht achterblijven).
Opgesloten lucht zal resulteren in holtes en luchtbellen in het gegoten plastic onderdeel, onvolledige vulling of oppervlaktedefecten zoals vlekken of brandplekken.
De volgende ontwerpregels voor spuitgietmatrijzen kunnen worden gebruikt om het gebrek aan luchtinsluiting tot een minimum te beperken:
- Evitar cambios de espesor grandes.
- Localizar las rejillas de ventilación en las últimas zonas del molde que se llenan.
- Localizar las puertas de entrada en las zonas que consigan que los puntos del molde que se llenan al final del ciclo posean una zona de aireación adecuada.
- Asegurar un tamaño de las zonas de aireación lo suficientemente grande para que el aire presente en la cavidad pueda escapar durante la inyección aunque ésta no debe de ser tan grande que produzca la salida del polímero fundido generando una rebaba. El tamaño de las zonas de aireación recomendado es de 0,025 mm para polímeros cristalinos, y 0,038 mm para los polímeros amorfos.

• Verlaag de injectiesnelheid. De hoge snelheden van kunststofinjectie kunnen het «jet»- of jetting-effect veroorzaken, waardoor ingesloten lucht direct bij de toegangsdeur verschijnt. Door de injectiesnelheid te verlagen, krijgt de lucht die bij de inlaat wordt verplaatst voldoende tijd om door de beluchtingszones te ontsnappen.
Laslijnen en verbindingslijn
Een laslijn (ook lasmarkering genoemd) wordt gevormd wanneer twee stroomfronten van gesmolten polymeer die in tegengestelde richtingen bewegen, elkaar ontmoeten. In plaats daarvan wordt een tieline geproduceerd als die twee fronten evenwijdig aan elkaar vloeien en een tieline creëren.
Traditioneel wordt de verbindingshoek tussen de twee vlakken gebruikt om laslijnen van verbindingslijnen te onderscheiden. Een verbindingshoek van minder dan 135º levert een laslijn op, terwijl een verbindingshoek van meer dan 135º wordt gedefinieerd als een verbindingslijn. In het algemeen verdwijnt een laslijnmarkering wanneer de verbindingshoek tussen 120° en 150° ligt. Laslijnen worden als kritischer beschouwd dan voeglijnen, zowel wat betreft de esthetiek als de mechanische eigenschappen van de verbinding.
Laslijnen en verbindingslijnen kunnen worden veroorzaakt door gaten of inzetstukken in het onderdeel, meervoudige pakking, of door gebieden met verschillende wanddikte waar aarzeling of race-tracking optreedt.
Indien las- of verbindingslijnen niet kunnen worden vermeden, is een goede praktijk dat deze ontstaan op slecht zichtbare of mechanisch niet-kritische plaatsen. Dit wordt vaak gedaan door de kunststof injectiepoort te wijzigen, de stroomfronten en de gebieden waar de las/naadlijnen voorkomen te veranderen. Een andere praktijk is te proberen een goede verbinding tussen de twee fluxen tot stand te brengen, zodat de mechanische zwakte die optreedt niet te groot is. Hiertoe is het de bedoeling dat het samenkomen van de twee stroomfronten plaatsvindt bij de hoogst mogelijke temperatuur en druk, zodat zij zich niet ver van de inlaatpoort bevinden.

De volgende aanbevelingen kunnen worden gebruikt om de impact van laslijnen en voeglijnen op spuitgietonderdelen te verminderen.
- Ajustar la posición de la puerta de inyección para producir las líneas de soldadura / unión en zonas de baja visibilidad o de bajas exigencias mecánicas.
- Permitir que las líneas de soldadura / unión se formen a mayor temperatura y mayor presión. Para ello, se recomienda: o Aumentar la temperatura de inyección. o Aumentar la velocidad de inyección. o Aumentar la presión de inyección.
- Aumentar el espesor de pared. Esto facilitará la transmisión de la presión y el mantenimiento de una temperatura de fusión superior.

Braam
De braam is een defect dat optreedt wanneer een deel van het gesmolten polymeer door de openingen in de spuitgietmatrijs stroomt, zoals het scheidingsvlak, beluchtingszones, uitstoters, enz. De braam treedt om de volgende redenen op:
- Baja fuerza de cierre de las mitades del molde. Si la fuerza de cierre de la máquina de inyección es demasiado débil para sostener las placas del molde juntos durante el proceso de moldeo, parte del polímero inyectado en la cavidad saldrá por el plano de partición generándose rebaba.
- Resquicios entre las mitades del molde de inyección. Si la superficie de separación de los moldes no entran en contacto por completo durante el cierre del molde (p.e., molde deformado) se generará un defecto de rebaba.
- Condiciones de inyección del plástico inadecuadas. Condiciones como temperatura de inyección excesiva (el polímero está más fluido y tiene más facilidad de fluir por los resquicios del molde), o elevadas presiones de inyección.
- Sistema de aireación inadecuado. Cuando es excesivo el tamaño de las salidas de aire en el molde, se producirá rebaba justo en esas zonas.
Als we alleen injectievariabelen beschouwen, kunnen de volgende correcties worden aangebracht om het probleem van flitsopwekking te minimaliseren.
- Aumentar el tamaño de la máquina de moldeo por inyección. La rebaba puede ser debido a un problema de insuficiencia en la fuerza de cierre de la máquina.
- Ajustar la fuerza de cierre si la capacidad de la máquina lo permite.
- Disminuir la temperatura de inyección. Una temperatura elevada reduce la viscosidad del polímero fundido haciendo más fácil que éste fluya por los resquicios del plano de partición, expulsores o zonas de aireación.
- Reducir la presión de inyección y de compactación para reducir la fuerza de cierre requerida.
- Aumentar el tiempo de inyección o ralentizar la velocidad de inyección para reducir la presión de inyección y así reducir la fuerza de cierre requerida.
Dimensionale samentrekkingen, kromtrekkingen en wendingen
Maatkrimp van onderdelen is inherent aan het spuitgietproces. Krimp treedt op omdat de dichtheid van het polymeer varieert van verwerkingstemperatuur tot kamertemperatuur (zie bijvoorbeeld het specifieke volume van een semikristallijn polymeer in Figuur 5.46 – PVT-curve). Tijdens de stadia van het spuitgietproces veroorzaakt koelkrimp een reeks interne spanningen in het onderdeel. Deze restspanningen werken op de kant met effecten die vergelijkbaar zijn met mogelijke extern uitgeoefende spanningen. Als de restspanningen die tijdens het gieten worden veroorzaakt hoog genoeg zijn, kan het onderdeel nadat het uit de mal is geworpen, kromtrekken/draaien of verdraaien, wat resulteert in defecte onderdelen.
Daarom is het kromtrekken of draaien van een kunststof injectieonderdeel te wijten aan het bestaan van een reeks resterende interne spanningen in het onderdeel die op hun beurt worden gegenereerd door de differentiële samentrekking van het materiaal tijdens het afkoelen. Als de krimp door het hele onderdeel uniform is, kromtrekt of verdraait het resulterende onderdeel niet, het krimpt gewoon gelijkmatig en wordt kleiner. Kristallijne polymeren, bijv. acetaal, nylon, polyethyleen met hoge dichtheid, polyethyleentereftalaat en polypropyleen veroorzaken de ernstigste problemen met krimp van 1 tot 4%. Amorfe polymeren, bijvoorbeeld polystyreen, acryl en polycarbonaat, zijn beter behandelbaar, met een krimp van slechts 0,3 tot 0,7%.
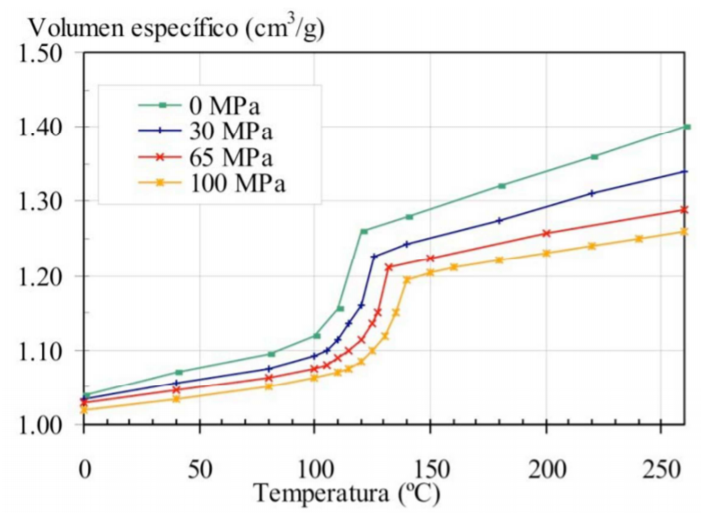
Het bereiken van een gelijkmatige krimp is echter gecompliceerd vanwege de aanwezigheid en interactie van vele factoren zoals de oriëntaties van de polymeermoleculen, temperatuurvariaties in de matrijswanden, verdichtingsvariaties in de kunststof onderdelen (zones met oververdichting en gebieden met lage verdichting , vanwege paden van onevenwichtige stromen), enz. Merk op dat de gebieden met grotere verdichting, zoals injectiedeuren, minder samentrekking hebben, aangezien een deel van de verdichting van het gesmolten polymeer dit compenseert. Aan de andere kant zijn de gebieden die het verst van de toegangsdeur verwijderd zijn onderhevig aan minder verdichting en hebben daarom de neiging om sterker samen te trekken.
Een vuistregel om buitensporige vervormingen in het onderdeel als gevolg van temperatuurverschillen na injectie te voorkomen, is dat de gemiddelde temperatuurverschillen in enig deel van het onderdeel na injectie niet groter mogen zijn dan 15-20ºC.
Enkele corrigerende maatregelen om het probleem van kromtrekken en verdraaien van spuitgietonderdelen te verminderen zijn:
- Evitar secciones gruesas. Las secciones gruesas en la pieza producen una importante contracción al enfriar. El uso de nervios y espesores uniformes produce una uniforme contracción de la pieza y reduce el coste y el peso de la pieza manteniendo su resistencia mecánica.
- Flujos balanceados. El sistema de inyección ha de generar flujos de material balanceados con una velocidad de flujo constante.
- Una presión de compactación adecuada puede compensar en parte la contracción del polímero al enfriarse.
- Localizar las puertas de entrada en las zonas de la pieza de mayor sección.
- Incrementar el tiempo de enfriamiento.
- Incrementar la temperatura de inyección. El empleo de bajas temperaturas de inyección hace que el material solidifique rápidamente sin tener tiempo a compactarse lo suficiente, lo que produce una contracción elevada. Algunos de los factores anteriormente citados y su efecto en la contracción final de la pieza se recogen en la figura siguiente.
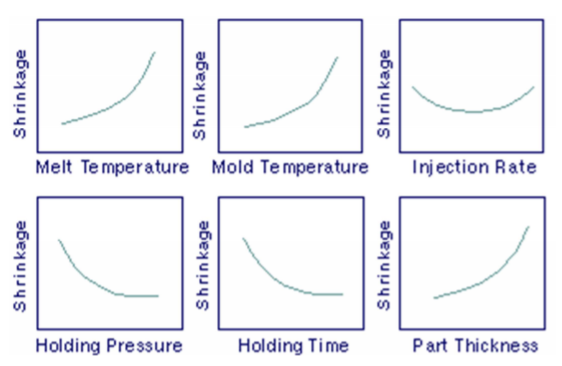
Slechte oppervlakteafwerking (vloeisporen, rimpels, golving, enz.)
Een slechte afwerking kan worden veroorzaakt door de vorming van rimpels of golven aan de randen van het onderdeel of in de laatste vullingsgebieden tijdens injectie.

De vorming van rimpels of golven is te wijten aan het feit dat een deel van het stroomfront snel afkoelt op de wanden van de mal, waardoor een vouw ontstaat op het stroomfront zelf. De belangrijkste factoren die de vorming van deze rimpels beïnvloeden, zijn onder andere de stroomsnelheid, de temperatuur van de wanden van de mal en de temperatuur van het gesmolten polymeer.
Sommige van de acties die moeten worden uitgevoerd om de oppervlakteafwerking te verbeteren, houden verband met acties om de stroomsnelheid en de temperatuur van het gesmolten polymeer en de matrijswanden te verhogen. Daarom wordt de verbetering van de oppervlaktekwaliteit bereikt met maatregelen zoals:
- Incrementar la temperatura del molde.
- Incrementar la velocidad de inyección, lo que incrementa la temperatura del polímero fundido por efecto de cizallamiento y reduce la viscosidad del mismo.
- Incremento de la presión de inyección.
- Incremento de la temperatura de inyección.

«Jet» defect
Het straaldefect of «jetting» treedt op wanneer het gesmolten polymeer met hoge snelheid door een klein gebied wordt geduwd, zoals het injectiemondstuk of de injectiedeur, om toegang te krijgen tot een veel groter gebied. Het explosiedefect veroorzaakt een mechanische zwakte in het onderdeel, onvolkomenheden in het oppervlak en meerdere interne defecten.

Om het straaleffect te minimaliseren, kunnen de volgende corrigerende maatregelen worden genomen:
- Reducir la velocidad de inyección en las zonas de cambio brusco de área.
- Uso de puertas de entrada de tipo “tab gate” o “fan gate”, que producen una transición más suave entre el canal de alimentación / bebedero y la cavidad del molde.

- Aumentar el tamaño de la puerta de entrada y del canal de alimentación.
- Ajustar el perfil de inyección de modo que la velocidad disminuya cuando el polímero fundido entre en la cavidad del molde para posteriormente acelerarse. La Figura 5.52 muestra un ejemplo de perfil de inyección con estas características.
