To create any plastic part using the plastic injection method, a metal mold is needed, that’s for sure.
The questions to ask are:
- How to design an injection mould?
- What is required to take into account when designing a mold?
- How does an injection mold work?
When it comes to the construction of a plastic injection mold, knowing how to choose the number of cavities can lead to more doubts. If the plastic piece is very large (chairs, urban planning fences, seats, etc.) the choice of 1 cavity is quite obvious, due to their size, another case is that of the pieces of which you want to make a short run, so there is no need to make the mold more expensive and 1 cavity is chosen.
To make large runs or when high production needs to be done in a short time, you can choose the multi-cavity option, to manufacture as many pieces as there are cavities in the mold in the same injection. .
Another clear case of multiple cavities is the assumption that it is necessary to manufacture several different small pieces, in which making a mold for each piece would be very expensive, in this case the multi-cavity is the most logical and economical option.




In the event that an injection mold with a single cavity is needed, its distribution and design is simple. But what happens when a multi-cavity mold is needed? How are they distributed? Is it done randomly? Are there better and worse ways to place the cavities? What is required to take into account when designing a mold?
The answer is that there is a whole science behind this and, as in this whole world of plastic injection, nothing is left to chance.
The first thing is to calculate how many cavities are needed, since this will define their distribution. The golden rule of injection molds with several cavities is that it be as symmetrical as possible, so that the plastic reaches all the pieces and fills them at the same time and alike. If the cavities are poorly distributed, some pieces would be filled before others, so either the cycle time is lengthened or one of the pieces will come out without sufficient cooling and with defects. This plastic injection process is not simple, since the more cavities that are needed, the more complicated its distribution is. Not only that, but as the channels get larger, the plastic loses pressure and temperature as it moves away from the main trough. In the following images you can see qualitatively this event.
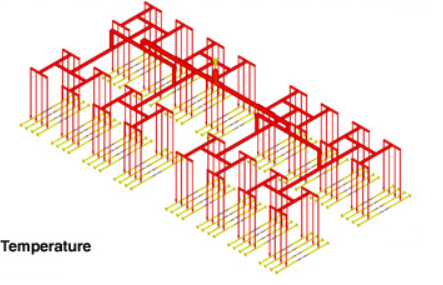

To design the plastic injection mold you have to know and answer these questions;
- How is an injection mold measured?
- How to calculate the area of a mold?
- How to calculate the injection speed?
- How to calculate the closing force in a mould?
- How to calculate the injection volume?
- What is the cavity of a mold?
There are several ways to distribute the cavities according to the needs of the Injection mold, always seeking a balanced flow and reducing material consumption. Many feeding systems use a mixture of radial and branching designs. The radial design has a lower feed system volume and provides a more balanced flow. However, longer primary channels and more debris are needed as the size of the cavities increases.
In the following image, you can see different types of radial distribution. As can be seen, the number of options for placing the cavities is extremely high and to choose the optimal one, different types of distributions are usually tested and filling analyzes are carried out to check their behavior.

Another equally valid way is to place the cavities with straight lines creating branches. It must be taken into account that, while for the radial type the number of cavities can be even or odd, for the branch type the number of cavities must be even, since otherwise it would be unbalanced.

Although there are multiple ways to place the cavities in a plastic injection mold, not all of them are acceptable or can be improved, since the cavities of the injection mold planes, although a priori they may seem symmetrical and valid , when you think about it carefully, the placement will cause the pieces to not be identical to each other. In the following examples the placement on the left is the wrong one and the one on the right improves it.
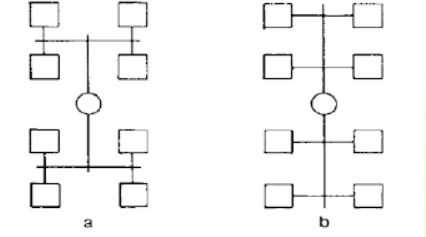
In this first case, it is quite clear that in the image on the left the flow would not reach all the cavities at the same time. It would first reach the 4 cavities closest to the injection mold sprue and, later, the other 4 furthest away, thus creating unequal parts. This can be fixed by changing the layout, as seen in the image to the right. With this change, all the cavities are identical.
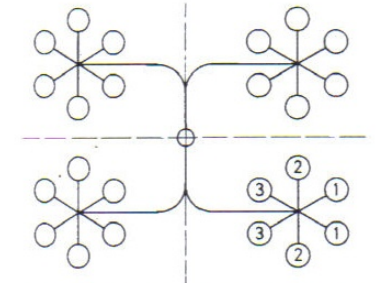

In the second case, it seems that the distribution is correct, since it is symmetrical and it seems that the flow arrives at the same time, but it is necessary to take into account not only the distance but also the direction it leads, since you have to remember that it is a molten plastic and carries an inertia. Therefore, the cavities with the number 1 will be the first to be filled, then those with the number 2 and finally those with the number 3, thus creating inequalities. This can be improved by changing the distribution to that of the image on the right, in which both the distance to each cavity and the flow inlet shape are the same.
Another less recommended way to balance the flow in the cavities is by increasing or reducing the feed channels. It is a practice that, although it can be successful, can also lead to problems. Naturally balanced feed systems (by cavity distribution) provide greater cavity-to-cavity consistency with respect to melt flow, melt pressure, and casting quality than artificially balanced designs (by changing the diameter of the holes). channels or inputs).
This practice is especially used in the manufacturing of different small plastic parts in the same plastic injection mold. With this practice, many pieces of a set can be made, with the only cost of making a mold instead of having to make one per piece, with which the savings are enormous. As is logical, calculations must be made so that all the cavities are balanced, so in principle putting all the channels and inputs the same would not be an optimal placement.

The difference between a balanced plastic injection mold and an unbalanced one is very noticeable. The first image shows a filling time of 10.24 seconds and irregular filling, while in the second image, with balanced inputs, it is seen that the filling is uniform and the filling time is noticeably lower. , 8.04 seconds. The difference is more than 2 seconds.


Once the decision has been made on how to place the cavities, you have to think about how big the channels that feed all the cavities have to be. As is logical, the channels do not have a constant diameter, at the beginning of the system they are notably larger than as the different branches are created, since the flow of plastic that they have to transport is less as they move away from the main trough . Making them all the same size would be inefficient, as it would result in more plastic being needed for each injection, and furthermore, that plastic would be waste. Not only that, but increasing the size of the channels would make them have a larger surface in contact with the metal of the mold, causing the plastic to cool quickly, potentially clogging them.
If you have doubts about the design of the cavities in an Injection Mold, at Moldblade we are specialists in Design, Manufacture of molds and Manufacture of plastic parts by plastic injection.